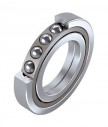
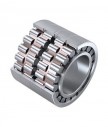
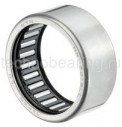
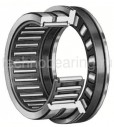
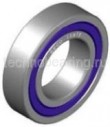
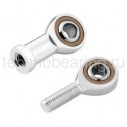
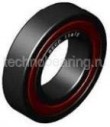
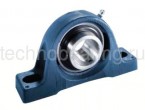
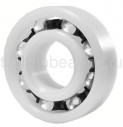
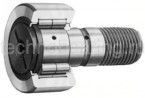
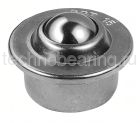
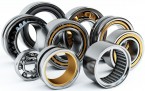
Опорный коэффициент динамической нагрузки
При расчете размеров подшипников качения применяется опорный коэффициент классификации динамической нагрузки C. Данный параметр выражает максимально допустимую нагрузку подшипника, способного выдержать номинальную долговечность, равную 1.000.000 оборотов. Опорные коэффициенты динамической нагрузки подшипников ISB® определялись согласно стандартам ISO 281. Учитывая опорные коэффициенты динамической нагрузки, определяется период эксплуатации, необходимый для появления признаков усталости материалов, на основе которого установлен теоретический срок службы.
При вращении на низких скоростях, уменьшенных движениях качения или применении подшипников на стационарных узлах, учитывается опорный коэффициент статической нагрузки C0. Опорный коэффициент статической нагрузки представляет собой восприятие нагрузки подшипника в состоянии покоя. Соответствует нагрузке трения, рассчитанной между наиболее нагруженным телом качения и дорожкой качения, равной:
- 4600 Н/мм2 для самоустанавливающихся шарикоподшипников.
- 4200 Н/мм2 для иных типов шарикоподшипников.
- 4000 Н/мм2 для всех типов роликоподшипников.
Данная нагрузка приводит к пластической деформации тела и дорожки качения, составляющей приблизительно 1/10000 (0,0001 dw) диаметра тела качения. Простой и радиальный тип нагрузки предназначен для радиальных подшипников, а простой и осевой тип нагрузки - для упорных подшипников.
Коэффициент статической нагрузки
Когда подшипник находится в состоянии покоя или подвержен нагрузке на небольших частотах вращения (ниже 10 оборотов/минуту), коэффициент статической нагрузки не устанавливается в отношении усталости материала, а на основе пластической деформации, вызванной в точке соприкосновения между телом и дорожкой качения. Данное правило имеет значение и в случае подшипников качения, подверженных тяжелым ударным нагрузкам, развивающимся во время одной доли оборота. В основном, величина нагрузки может увеличиться до коэффициента статической нагрузки C0, не изменяя рабочих характеристик подшипника. Комбинированную статическую нагрузку (одновременное действие радиальной и осевой нагрузки) нужно превратить в эквивалентную статическую нагрузку. Такой тип нагрузки определяется как нагрузка (радиальная для радиальных подшипников и осевая - для упорных) которая, в случае применения, могла бы привести подшипник к одинаковой пластической деформации, вызываемой реальными условиями нагрузки.
Эквивалентная статическая нагрузка определяется по формуле:
В опорах современных механизмов и машин широко используют подшипники качения. Как правило, применение подшипников является более экономически обоснованным, чем использование других видов опор. Однако степень экономичности может колебаться в зависимости от выбора подшипника как по конструктивной разновидности, так и по размерам из-за того, что в итоге могут существенно изменяться расходы на материалоемкость узла, срок его службы, эксплуатацию и т. д.
Анализ перспективы применения подшипников качения показывает, что в ближайшие десятилетия альтернативы им не будет. Обладая рядом преимуществ перед другими опорами осей и валов в машинах и механизмах, таких, как малый коэффициент трения, простота монтажа и эксплуатации, относительная дешевизна, подшипники качения получили широкое распространение. В настоящее время количество ежегодно изготавливаемых в мире подшипников измеряется несколькими миллиардами штук. Поэтому понятно, какое большое экономическое значение имеют научно-исследовательские работы, направленные на решение проблемных вопросов, связанных с применением подшипников качения (ограниченные сроки их службы при высоких скоростях и нагрузках, снижение рассеивания показателей их долговечности). За последние три десятилетия несомненные успехи в направлении улучшения качества материалов, используемых для изготовления подшипников, совершенствования их конструкции и технологии изготовления, позволили существенно повысить их работоспособность, быстроходность и тем самым снизить габариты узлов, расширить сферу применения. Однако требования увеличения мощности и скорости машин при одновременном уменьшении их массы, а также повышения точности массовых подшипников и снижения уровня их шума и вибрации для электронно-вычислительных машин, бытовой и видеотехники диктуют необходимость дальнейшего совершенствования подшипников качения.
Потребительские свойства подшипников должны удовлетворять различным условиям эксплуатации. Если, например, в сельскохозяйственных машинах до 90% подшипников выходят из строя вследствие загрязнений, то 80% подшипников коренного вала газотурбинного двигателя самолетов бракуют в результате точечной коррозии. Подшипники подвижного состава железных дорог или лесопильных рам выходят из строя как по усталостному выкрашиванию, так и по сколам, трещинам колец и сепараторов. Поэтому важной задачей является изучение факторов, препятствующих подшипнику достичь теоретической долговечности. Любой другой выход подшипника из строя необходимо рассматривать как потери, экономически необоснованные.
В данной работе рассмотрены опоры трения качения с позиций современного состояния вопроса, причем внимание акцентируется главным образом на совершенствовании их расчета, применения и эксплуатации. Дан расчет базовой динамической грузоподъемности разных конструктивных групп подшипников с учетом последних исследований с использованием повышающих коэффициентов. При расчете статической грузоподъемности наряду с традиционным выводом зависимостей описаны результаты новых исследований, позволивших существенно увеличить статическую грузоподъемность, особенно роликоподшипников. Систематизированы причины, влияющие на уровни шума и вибрации подшипников, даны рекомендации по их устранению.
Важнейшее условие нормального функционирования подшипника — смазка — рассмотрено с точки зрения упругогидродинамической (УГД) теории. Приведены зависимости, позволяющие определить толщину слоя смазки как для линейного, так и для эллиптического контакта. Показан зарубежный опыт выбора коэффициента материала и условий эксплуатации для разных режимов работы подшипника и данной смазки, а также предложены рекомендации по выбору требуемой вязкости смазки в зависимости от режима эксплуатации подшипника. В работе рассмотрены физические различия контакта на жидкой и пластичной смазках, на основе исследований и опыта эксплуатации приведены соответствующие рекомендации. Описаны причины выхода подшипников из строя и возможные способы его предупреждения.
Под подшипником качения понимают простейший узел, в котором между поверхностями вращающейся детали и поверхностью опоры расположены тела качения, обычно шарики или ролики. Однако этот простой малоэлементный механизм требует многих видов расчетов, часто сложных и фундаментальных.
Если нагрузка на подшипник направлена перпендикулярно оси вращения кольца, то ее называют радиальной, а подшипники, предназначенные для восприятия таких нагрузок,— радиальными. Ось вращения тел качения радиальных подшипников в принципе параллельна оси вращения колец. В случае когда нагрузка на подшипник направлена под углом к оси вращения кольца, ее можно разложить на составляющие: радиальную и осевую. Иногда такую нагрузку называют комбинированной. Для восприятия подобных нагрузок существуют подшипники, которые в зависимости от отношения нагрузок по мере его роста называют радиально-упорными или упорно-радиальными. Ось вращения тел качения указанных подшипников пересекает под углом ось вращения колец. Если нагрузка на подшипник направлена по оси вращения кольца, то ее называют осевой, а подшипники, предназначенные для восприятия таких нагрузок,— упорными. Ось вращения тел качения этих подшипников перпендикулярна оси вращения колец.
Приведенное разделение подшипников по направлению воспринимаемой нагрузки относительно оси вращения колец не означает, что, например, некоторые виды радиальных подшипников нельзя применить для восприятия комбинированной или осевой нагрузки. Многое здесь зависит от величины нагрузки, частоты вращения и смазки. Действующие стандарты конкретизируют использование подшипников в зависимости от направления нагрузок.
По форме тел качения подшипники разделяют на две большие группы: шариковые и роликовые. В целом можно утверждать, что для малых и быстроходных узлов со сравнительно низкой нагрузкой чаще используют шариковые подшипники, а для больших тяжело нагруженных узлов — роликовые. Шарико - и роликоподшипники разделяют на значительное число конструктивных групп.
Подшипники качения обычно состоят из внутреннего кольца, наружного кольца и тел качения (шариков или роликов), а также сепаратора, который используется для позиционирования тел качения через определенные интервалы между дорожками качения кольца.
Стандартными материалами для внутреннего и наружного колец, а также для тел качения являются высокоуглеродистая хромистая подшипниковая сталь или закаленная сталь. Данная сталь подвергается термообработке до соответствующей прочности, чтобы достичь оптимального сопротивления усталости при прокатке.
Поверхности подшипников выравниваются с очень высокой точностью с помощью специальных механических инструментов. Несмотря на то, что каждый из множества типов подшипников качения обладает специфическими особенностями, следующие особенности являются общими для большинства типов подшипников качения:
Подшипники качения обладают относительно низким пусковым сопротивлением. Между пусковым сопротивлением и сопротивлением движению подшипников качения существует очень небольшая разница.
Размеры и точность стандартизованы. Получение готовых изделий высокого качества является легкодостижимым.
По сравнению с подшипниками “скольжения” подшипники качения менее предрасположены к износу, что способствует поддержанию точности механизма, в котором они используются.
При использовании подшипников качения потребляется небольшое количество смазки, и их эксплуатация обходится намного дешевле, чем эксплуатация подшипников скольжения. Для получения оптимального эффекта от использования выбранного подшипника необходимо понимать конструкцию и особенности различных типов подшипников, и в соответствии с ними выбирать подшипники, оптимальные для эффективности конкретного механизма.